For Railway
Our noise barrier provides the opportunity to reduce noise levels for residents along the railway without any noticeable impact on their living environment. This is achieved by placing our low-height noise barrier very close to the train. Its close proximity to the source of the noise allows it to reduce sound levels by 5-11 dB (depending on train type), despite being only 73 centimeters above the railhead.
The cost of a low noise barrier like Soundblock can be up to three times lower than traditional high barriers in terms of purchase, installation, and maintenance over a 50-year period.
The entity responsible for railway maintenance aims for a solution with minimal upkeep. A low barrier, placed on the railway embankment and on both sides of the track, may involve some additional maintenance costs. These costs can include extra procedures, snow removal, and sleeper replacements.
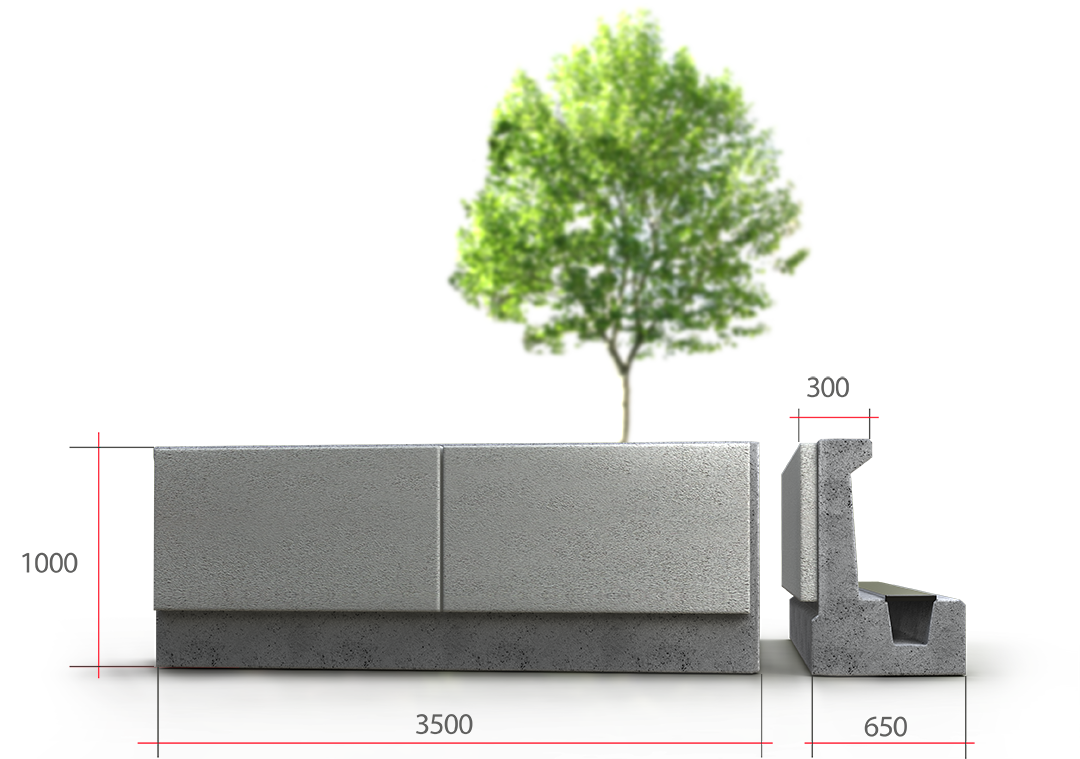
Compared to the maintenance costs of high barriers, the total cost of Soundblock remains significantly lower over a 50-year period, as the barrier itself is maintenance-free. To assist project planners in evaluating the total cost of Soundblock for a specific project, we have compiled insights and experience further down the page under the ‘Planning & Design’ section.
Regarding safety considerations, evacuation doors are available for emergency track exits. For efficient train evacuation, the upper section of the Soundblock serves as a platform. Additionally, specific procedures are often established for railway sections with low barriers on both sides of the track.
Function
The Soundblock noise barrier utilizes the ‘free space’ on the railway embankment, tackling noise at its source. Its core, made of fiber-reinforced concrete, effectively blocks sound waves. The absorber provides additional benefits, including channel damping and chamber damping, while also eliminating issues with sound reflections. The barrier achieves noise reduction of up to 11 dB.
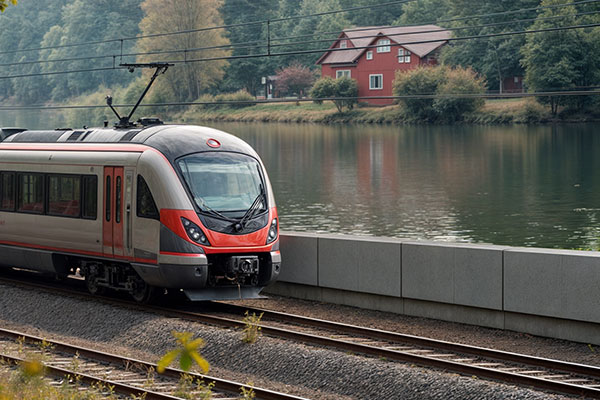
• Channel Damping
Due to the narrow gap between the train and the Soundblock barrier, a slit-shaped channel is formed where sound waves repeatedly reflect off the train’s side and are absorbed by the noise-absorbing material within the Soundblock barrier.
For high barriers placed further from the track (e.g., 4 meters) without sound absorption, repeated reflections can instead be detrimental to noise reduction.
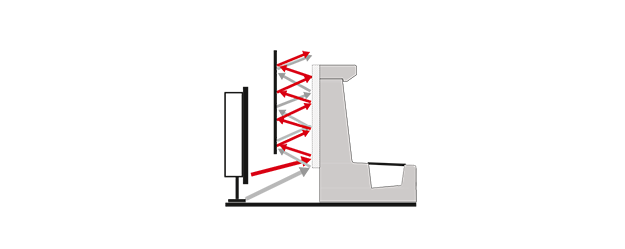
• Chamber Damping
Because the Soundblock noise barrier is positioned so close to the track and features a sound-absorbing interior, it creates a noise-dampening chamber within the bogie area. Soundblock effectively ‘encloses’ and ‘dampens’ this space, trapping noise partially under the train, where it is absorbed by the Soundblock barrier and the track ballast.
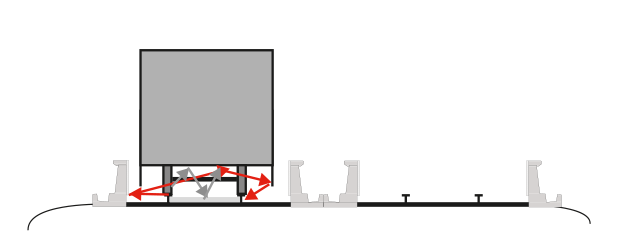
Safety
Soundblock can be equipped with doors, footrests, or ladders at desired intervals, and its top section is designed to facilitate safe evacuation from stationary trains.
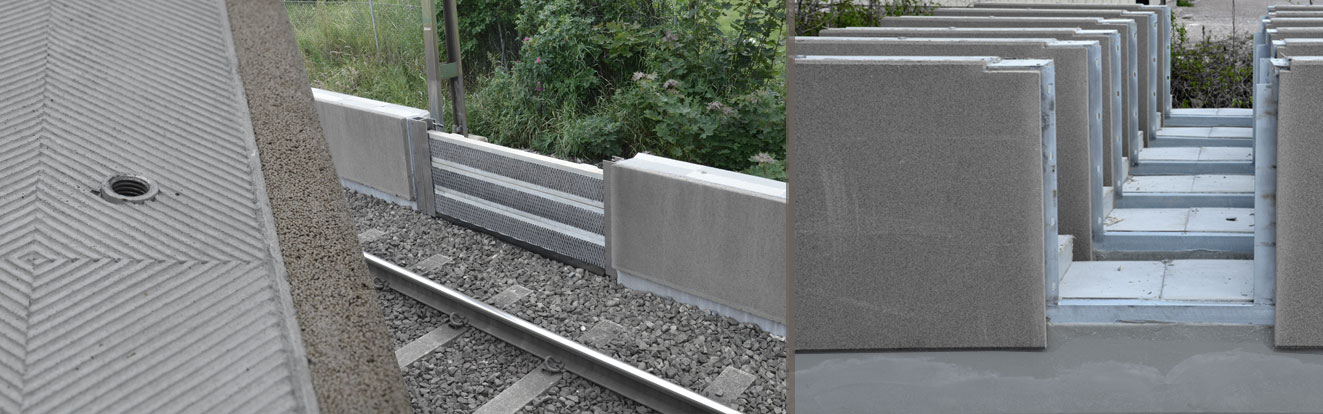
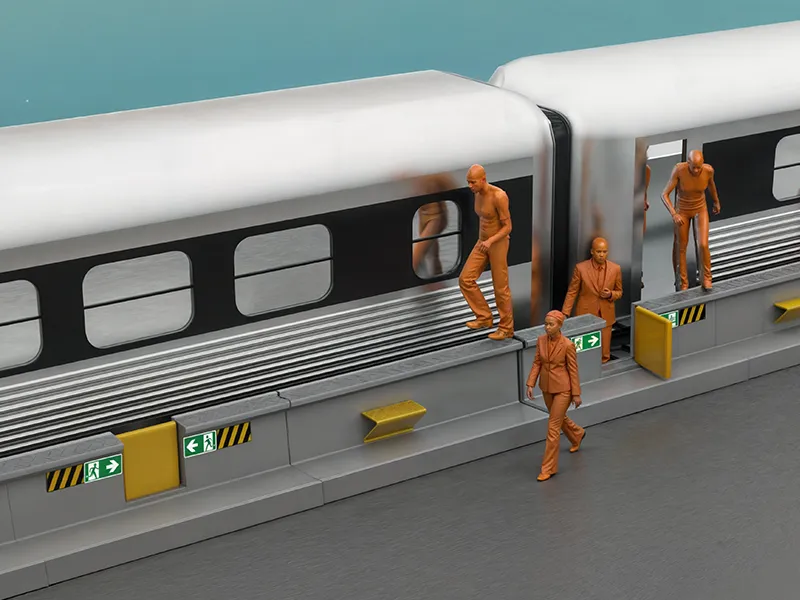
Simple Foundation
and Installation
STEP 1
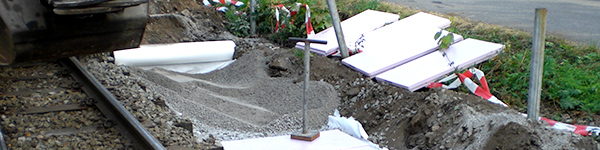
1. Excavate 20 centimeters from the railway embankment.
2. Lay down geotextile fabric (optional: cellular plastic).
3. Refill with crushed material.
STEP 3
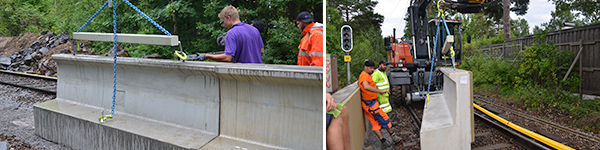
5. Install the sealing strip and place the Soundblock in position.
STEP 2
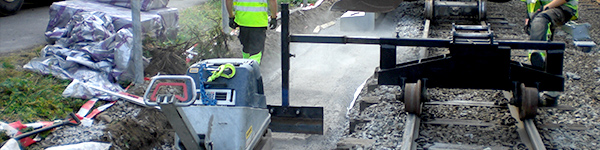
4. Create a level, compacted surface
STEP 4
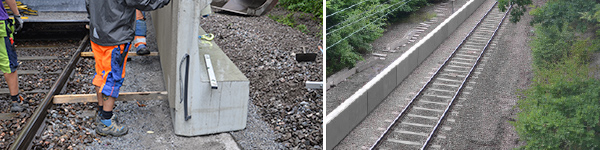
6. Check the distance from the track.
7. Done.
Foundation Example
The elements should be founded 270 mm below the railhead (RÖK). Geotextile fabric is placed 200 mm below the base plate of the Soundblock, followed by crushed material, which is compacted and leveled.
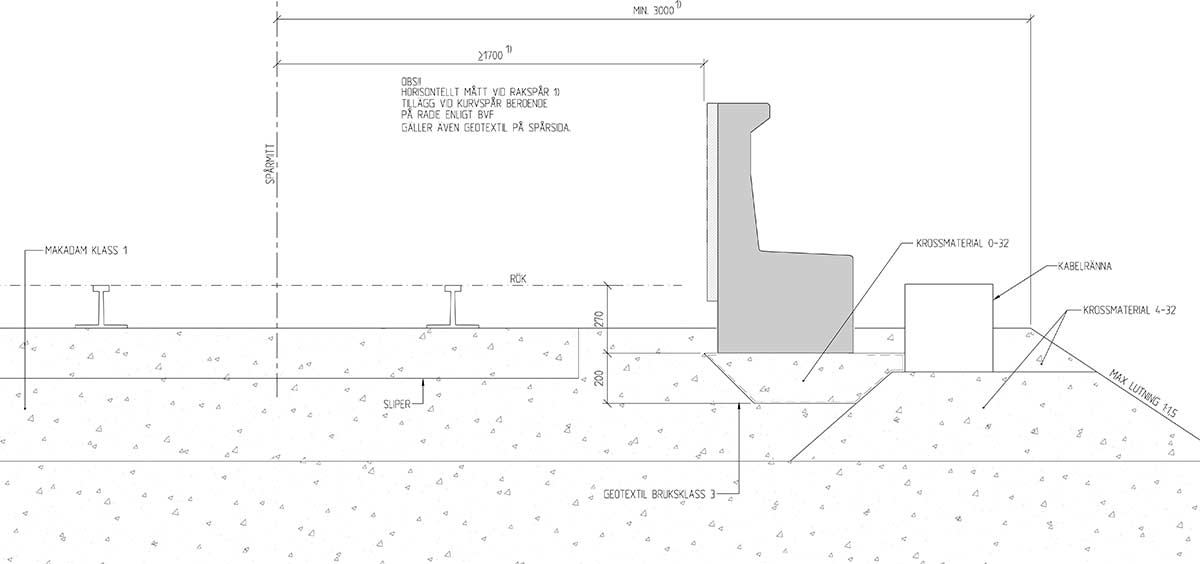
Placering på banvall (Soundblock 250)
1700 mm från spårmitt, tillägg för kurvspår i enlighet med BVF.
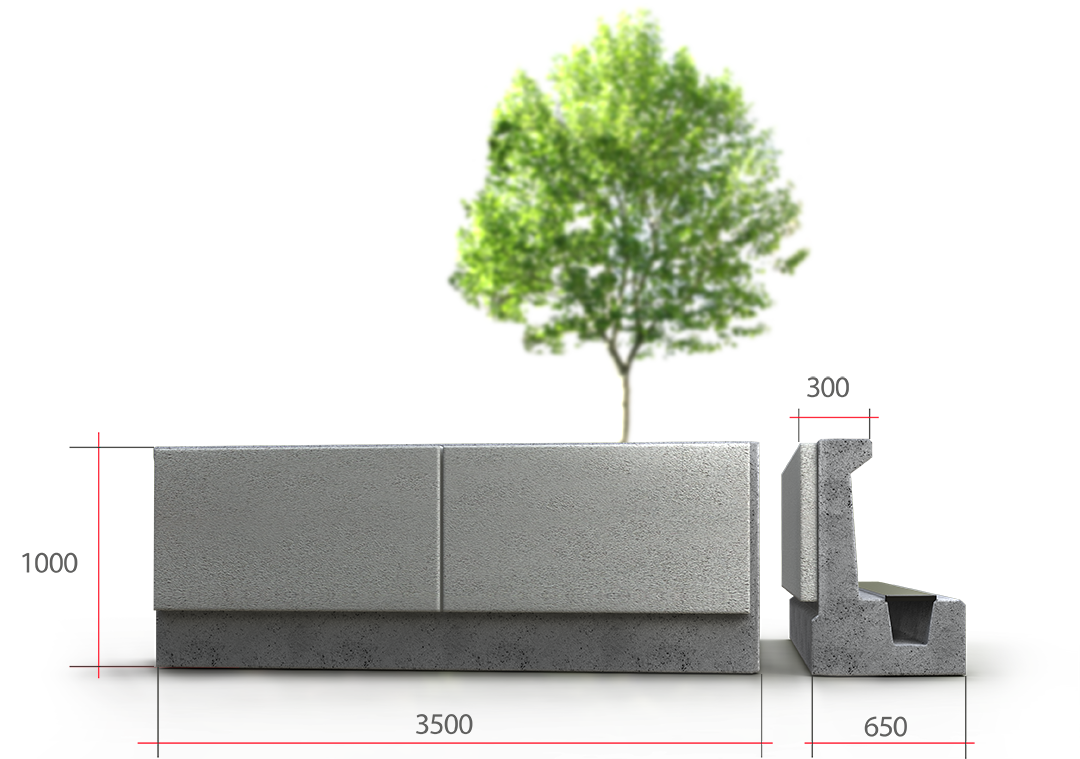
Installation
The lifting process is carried out using a yoke that hooks into two pre-attached lifting eyes, complemented by a balancing lift on the shelf. (The lifting eyes are attached before installation and removed afterward.)
Soundblock units are placed sequentially on the railway embankment. They do not require anchoring to the ground or to adjacent blocks, as their weight ensures stability. A sealing strip is installed between the blocks before placement. Additionally, individual blocks can be removed from the row if needed.
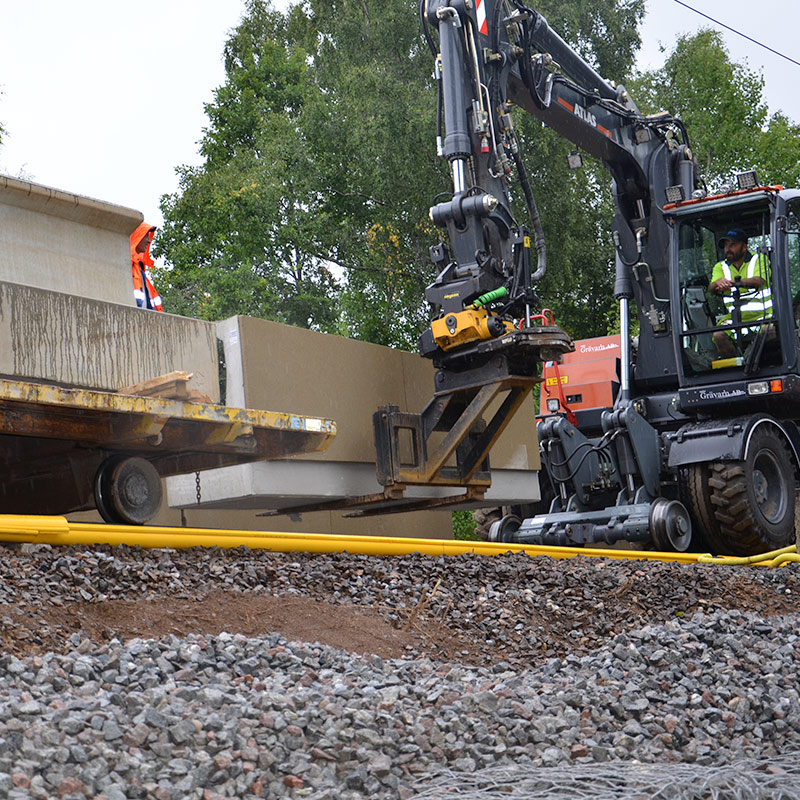
MANUFACTURING
Soundblock is manufactured using fiber-reinforced concrete.
This material choice enhances adaptability while also ensuring that no electrically conductive materials are used in the Soundblock elements.
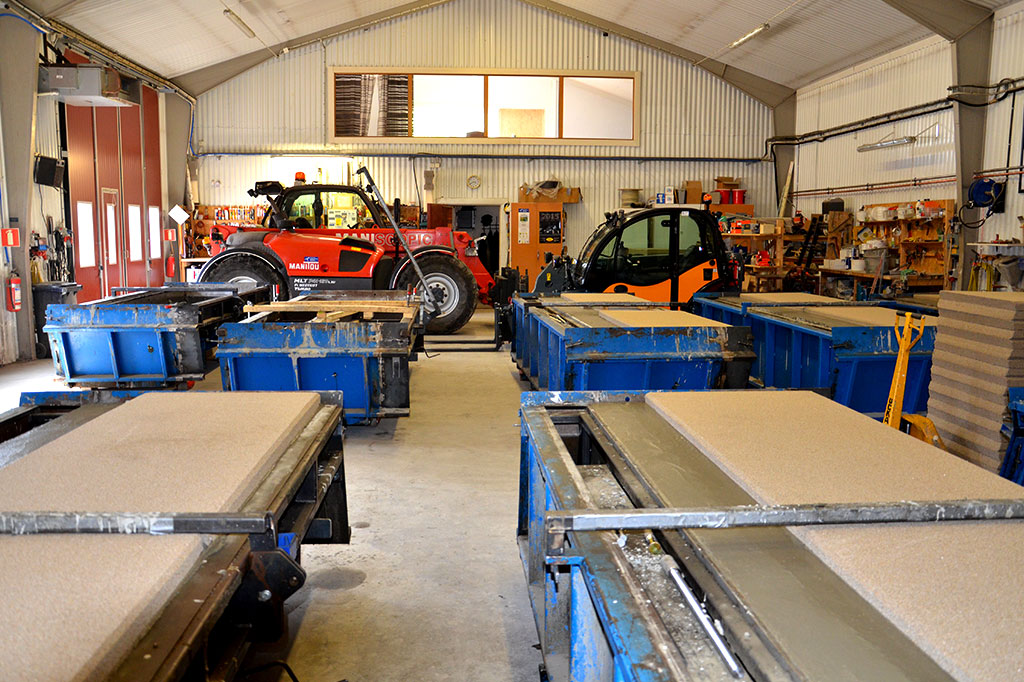
Various Setup
Options
Below are various setup options for Soundblock, adapted to different environmental conditions:

1. A single block is used when buildings are at the same level as or lower than the track. If similar buildings exist on the opposite side of the track, a single block is placed there as well.

2. Two Soundblocks are used when buildings are situated higher than the track.

3. A single block on each side along with a central barrier(s) when buildings are situated higher than the track on both sides.
Planning & Design
Since Soundblock has a low total cost, does not obstruct visibility, and provides effective noise reduction, it would be the only noise barrier used worldwide if there were no varying conditions influencing the choice of barriers.
What I can do—and strive to do—is assist those planning noise reduction measures in determining, as efficiently as possible, whether a low noise barrier is the best solution for a specific railway section.
Nicklas Erlandsson
Sales Manager
0708-321 680
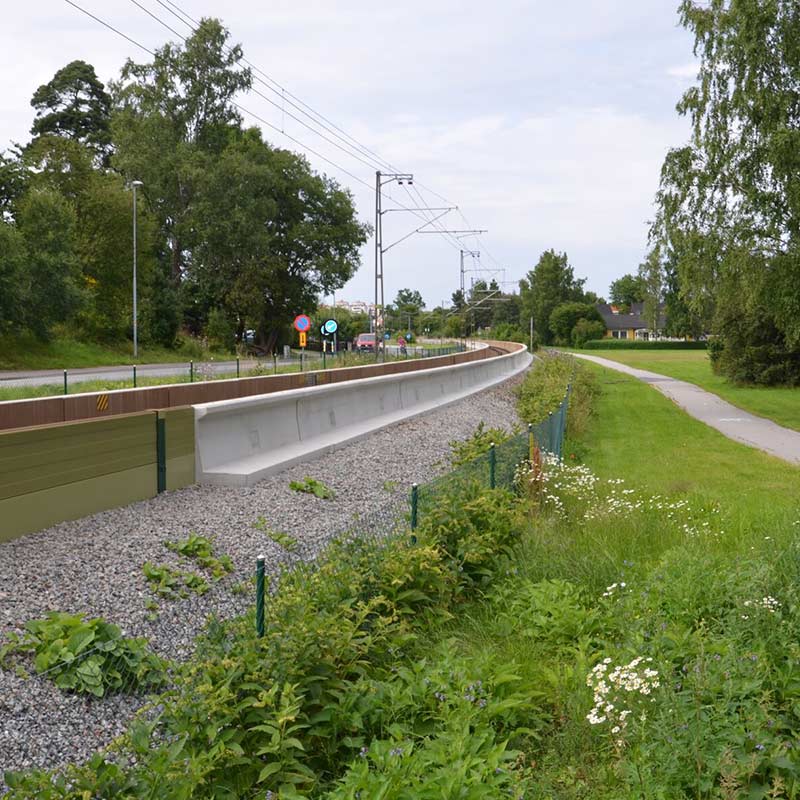
Key Considerations Before
Choosing a Low Noise Barrier
Summary
1. Acoustic requirements – Calculation data available for different train types
2. Estimating installation costs for Soundblock (e.g., whether the embankment needs to be widened, accessibility to the track area)
3. Estimating additional costs over a 50-year period (e.g., track work requiring blocks to be temporarily moved, snow removal routines, and extra procedures. These calculations are generally only necessary when low barriers are placed on both sides of the track, as Soundblock itself is maintenance-free).
Further details on these points are provided below:
1. The first step is to ensure that Soundblock meets the acoustic requirements for the relevant railway section. Assessing the acoustics of low barriers has always been a challenge. That’s why, in collaboration with Tyréns AB, we have developed a calculation model to facilitate this assessment. The model can be requested at Nicklas@zblocnorden.se.
Additionally, we can perform an initial acoustic assessment in collaboration with an acoustics consultancy to determine feasibility. Soundblock provides a stable noise reduction of 5-7 dB, depending on train type, regardless of the receiver’s location. In some cases, a 10-11 dB reduction can be achieved on specific sections. It is also useful to compare the height a traditional high barrier below the embankment would need to be versus a trackside barrier of just 73 cm above the railhead on a specific section.
2. Once we confirm that a low barrier meets the acoustic requirements, the next step is to evaluate the installation costs. With extensive experience in this area, we are happy to assist. Key questions include whether the embankment needs to be widened, the accessibility of the track, and the available working time per installation session.
We encourage you to share images and drawings of the site to help identify any necessary adjustments. Modifications may include integrating a cable trench into the Soundblock design or adjusting certain blocks during casting to accommodate existing railway installations on the embankment.
3. Finally, maintenance costs over the relevant period must be considered. The advantage of Soundblock in this context is that it can always be easily removed if needed. However, this is associated with a cost of approximately 2,000 SEK per meter for removal and reinstallation (depending on site accessibility).
When Soundblock is placed on both sides of the track, it may present challenges during maintenance operations such as ballast cleaning and sleeper replacement. These procedures, which require Soundblock to be temporarily removed, generally occur at long intervals (30-40 years). It is advisable to assess whether some maintenance work can be carried out at the time of installation to avoid major railway maintenance within 5-10 years after placement.
More frequent maintenance activities, such as using ballast plows, do not significantly impact maintenance costs—though extra caution may be needed. The conditions are exactly the same as those at railway platforms (same distance and height).
For snow removal, we recommend specifying in the procurement process that the contractor should have access to a rail-mounted snow blower. Including detailed snow removal procedures for low barriers in the procurement documents ensures fair and clear expectations for the contractor. Developing protocols for snow removal and safety procedures will naturally involve additional time and costs compared to traditional barriers. However, there is extensive experience in this area.
Special transports are another factor influenced by placing the noise barrier on the railway embankment. In simple terms, if a transport can pass by a platform, it can also pass by Soundblock. However, if the route is frequently used for special transports, a low trackside barrier may not be the most cost-effective solution.
Track accessibility may also change, but just like traditional noise barriers, which require designated openings for access, Soundblock includes doors at regular intervals.
For more detailed information and assistance with documentation, contact Nicklas Erlandsson at 0708-321 680 or nicklas@zblocnorden.se.
References
Below is a selection of reference projects.
Since 1999, Z-bloc Norden AB has delivered railway-adjacent noise barriers to the following locations: Karlstad, Karlskrona, Kramfors, Gustavsvik, Bollstabruk, Umeå, Kalix, Morjärv, Nynäshamn, Molnby, Umeå Central, Gimonäs (Umeå), Åby (Norrköping), Kristinehamns kommun, Annedal, Örnsköldsvik, Bro (Stockholm), Mölnbo, Södertälje, Sya (Mjölby kommun), Ritorp (Stockholm), Sollentuna Station, Täby kyrkby, Lagerlunda, Norra Järnvägsgatan (Boden), Skogås (Stockholm), Gimonäs (Umeå), Åby (Norrköping), Roslagsbanan, Saltsjöbanan, and Sundsvall.